expects to begin making led downlight on silicon wafers in about two years, a technology transition which promises to slash LED lighting costs.
The company today announced it has met performance targets for the new process which it projects could lower the cost of end-user lighting products by roughly 20 percent to 30 percent.
Bridgelux manufactures LED light sources, or chips, which are fitted into lamps and fixtures made by lighting companies. LEDs are more energy efficient and last longer than other lighting technologies, but the higher cost remains a barrier to mass adoption, particularly in the consumer market.
Right now, those LED chips are made by depositing thin films of semiconductor material onto a substrate made of sapphire or silicon carbide. To make led downlight, Bridgelux has been depositing the same material--Gallium nitride (GaN)--but on eight-inch silicon wafers. Fabricating on silicon will lead to lower costs because high-volume silicon-chip manufacturers can start making LEDs, said Brad Bullington, the vice president of corporate strategy and development at Bridgelux.
Researchers for years have been trying to perfect the process of manufacturing on silicon but have had problems with wafers cracking or bowing. Bridgelux claimed that it can produce GaN on silicon LEDs at the same performance as state-of-the art led downlight processes today.
With cool white light, its prototypes can achieve 160 lumens per watt (lumens is a measure of light output), while with warmer yellow light it can get 125 lumens per watt. For the warmer light, that chip efficiency translates into end-user LED bulbs with efficiency of 85 lumens per watt, which is higher than today's commercial products. Philips last week was awarded the L Prize from the Department of Energy for an LED lamp with efficiency of 90 lumens per watt, which is expected to be available next year.
"We could take this to market probably in the next 24 months, that's a realistic target and objective," said Bullington. "The biggest barrier to commercializing it is actually manufacturing it."
So far, Bridgelux has done batches using its process to "grow" layers of film on silicon wafers. When made at large scale, it could reduce the cost of led downlight--which are 40 percent of a bulb's cost--by about 75 percent, Bullington said. With lower LED chip costs, more lamp and light fixture companies will transition to LEDs, he predicted.
The company has been able to improve the performance of its chips in terms of lumens per watt, light color, and color rendering index which measures light quality. In March when it announced its GaN on silicon strategy, Bridgelux said it has achieved 135 lumens per watt for white light.
Bridgelux Hits LED Efficiency Mark in Move to Silicon | – L
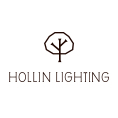
Public Date:
2011-08-10 13:46
Recent Arrticles